Hello everyone, and welcome back to the Cognixia podcast! Every week, we bring you fresh perspectives on the technologies that are reshaping our world, and today we have an absolutely electrifying episode lined up for you!
So, grab your morning coffee, settle into your favorite listening spot, and prepare to dive deep into the revolutionary world of Industrial Internet of Things transformation. We are talking about how the brightest minds in manufacturing – those forward-thinking CIOs who are steering some of the world’s largest industrial operations – are completely reimagining what it means to run a smart factory in 2025!
Picture this: you walk onto a manufacturing floor where machines don’t just follow pre-programmed instructions, but actually communicate with each other, predict their own maintenance needs, and even negotiate optimal production schedules in real-time. Collaborative robots work alongside human operators so seamlessly that it feels like watching a perfectly choreographed dance. Well, that future isn’t just a science fiction fantasy anymore – it’s happening right now, and the manufacturing CIOs leading this charge are the unsung heroes of our industrial revolution!
Today, we are unpacking the fascinating world of Industrial Internet of Things, exploring how it is transforming everything from automotive assembly lines to pharmaceutical production facilities. We will journey through the evolution from Industry 4.0 to the emerging Industry 5.0 paradigm, discover why collaborative robots are making traditional industrial automation look like yesterday’s news, and tackle the real challenges that keep manufacturing executives awake at night. Trust us, by the end of this episode, you will understand why IIoT isn’t just changing manufacturing – it is fundamentally redefining what industrial production means in the 21st century!
Let us begin by demystifying what Industrial Internet of Things actually means, because despite all the buzzword fatigue around IoT, IIoT represents something genuinely transformative. At its core, IIoT is about creating intelligent, interconnected manufacturing ecosystems where every machine, sensor, and system can communicate, share data, and make autonomous decisions to optimize production outcomes.
Think of traditional manufacturing as a symphony orchestra where each musician plays their part independently, following a rigid score. IIoT transforms this into a jazz ensemble where musicians listen to each other, respond dynamically, and create something beautiful through real-time collaboration. Your production line becomes a living, breathing organism that adapts to changing conditions, anticipates problems before they occur, and continuously optimizes itself for maximum efficiency.
The importance of this transformation extends far beyond individual factory floors. In our interconnected global economy, manufacturing efficiency directly impacts everything from the smartphone in your pocket to the electric vehicle in your driveway. When manufacturing becomes more intelligent, more responsive, and more efficient, it creates ripple effects that benefit consumers through better products, lower costs, and faster innovation cycles.
For the manufacturing sector specifically, IIoT represents the difference between surviving and thriving in an increasingly competitive landscape. Companies that master IIoT implementation can achieve dramatic improvements in operational efficiency, often seeing 20-30% reductions in unplanned downtime, 15-25% increases in overall equipment effectiveness, and significant improvements in product quality consistency. These are not just nice-to-have improvements – they’re often the difference between profitability and obsolescence in today’s hyper-competitive global marketplace.
What makes this moment particularly exciting is that we are witnessing a fundamental shift in industrial paradigms. The manufacturing world is transitioning from the Industry 4.0 era, which focused primarily on digitization and automation, toward Industry 5.0, which emphasizes human-machine collaboration and sustainable, personalized production.
Industry 4.0 was about making factories smart through connectivity and data analytics. It gave us predictive maintenance, real-time production monitoring, and automated quality control systems. But Industry 5.0 takes this evolution several steps further by reimagining the relationship between humans and machines in industrial settings.
In the Industry 5.0 paradigm, technology does not replace human workers – it amplifies their capabilities. We’re moving toward manufacturing environments where artificial intelligence handles routine decision-making and data processing, freeing human operators to focus on creative problem-solving, strategic thinking, and complex troubleshooting that requires intuition and experience.
This shift is particularly evident in the rise of collaborative robots, or cobots, which represent one of the most exciting developments in modern manufacturing. The difference between traditional robots and cobots is like comparing a powerful but inflexible bulldozer to a skilled assistant who can adapt to any situation. Traditional industrial robots excel at repetitive, high-speed tasks in controlled environments, but they lack the flexibility and intelligence to handle variability or unexpected situations. Cobots, on the other hand, combine the precision and consistency of automation with the adaptability and problem-solving capabilities that come from close collaboration with human operators.
What makes cobots particularly revolutionary is their ability to learn from human demonstration and adapt their behavior based on changing requirements. A cobot can watch a skilled technician perform a complex assembly task, learn the optimal techniques, and then replicate that expertise consistently while still maintaining the flexibility to handle variations in parts or processes.
However, the path to IIoT mastery isn’t without significant challenges, and one of the biggest obstacles facing manufacturing CIOs is the prevalence of legacy systems that were never designed to participate in connected, intelligent manufacturing environments.
Many manufacturing facilities operate equipment that was installed decades ago and designed for a completely different technological paradigm. These legacy machines often lack the sensors, connectivity, and processing capabilities needed to participate in IIoT ecosystems. Retrofitting this equipment while maintaining production schedules and ensuring safety standards represents a complex engineering and logistical challenge that requires careful planning and significant investment.
The challenge isn’t just technical – it’s also cultural and organizational. Many manufacturing organizations have deeply embedded processes and workflows that were optimized for traditional, disconnected operations. Transitioning to IIoT requires not just new technology, but also new ways of thinking about production planning, maintenance scheduling, quality control, and workforce management.
Perhaps even more challenging is the growing shortage of skilled professionals who understand both traditional manufacturing processes and modern digital technologies. The manufacturing sector needs workers who can bridge the gap between mechanical engineering and data science, between production line operations and cloud computing, between traditional quality control and AI-powered predictive analytics.
This skills gap is becoming increasingly critical as IIoT implementations become more sophisticated. It’s not enough to have technicians who understand how to operate machinery or IT professionals who understand networking and data management. Modern manufacturing requires hybrid professionals who can think across disciplines and understand how digital technologies can enhance and optimize physical production processes.
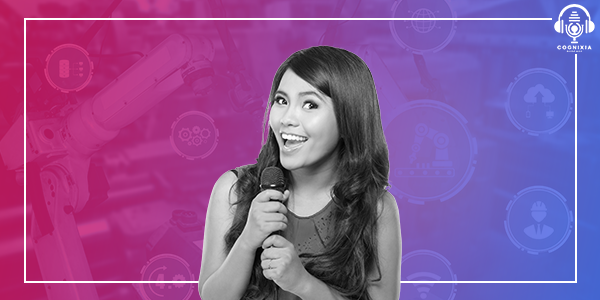
The solution to this skills challenge lies partly in comprehensive training and education programs, but it also requires a fundamental rethinking of how manufacturing roles are structured and defined. Forward-thinking companies are creating new job categories that blend traditional manufacturing expertise with digital technology skills, and they are investing heavily in upskilling their existing workforce.
One of the most exciting developments addressing these challenges is the emergence of agentic AI systems that can interact naturally with human operators through conversational interfaces. Instead of requiring workers to learn complex software interfaces or memorize numerous procedures, these AI systems can respond to natural language queries and provide intelligent guidance in real-time.
Imagine being able to walk up to any piece of equipment on your production floor and simply ask it questions like “What is causing the efficiency drop in line three?” or “How should I adjust the temperature settings to improve product quality?” Agentic AI makes this kind of natural interaction possible, dramatically reducing the learning curve for new technologies while making expert knowledge accessible to workers at all skill levels.
These conversational AI systems can serve as intelligent assistants that help workers troubleshoot problems, optimize processes, and make informed decisions based on real-time data analysis. They can provide step-by-step guidance for complex procedures, suggest optimization opportunities, and even predict potential issues before they impact production.
What makes this technology particularly powerful is its ability to learn from every interaction and continuously improve its understanding of specific manufacturing environments. An AI system that starts with general manufacturing knowledge can quickly develop deep expertise in the particular processes, equipment, and challenges of a specific facility.
Supporting this technological transformation is the development of comprehensive infrastructure platforms that make IIoT implementation more accessible and scalable. A particularly noteworthy example is Reliance Jio’s Lego-as-a-Service framework, which represents a fundamentally new approach to industrial technology deployment.
This innovative platform enables plug-and-play adoption of sophisticated IIoT solutions without requiring extensive custom development or integration work. Just as Lego blocks can be combined in countless ways to create complex structures, Jio’s framework allows manufacturers to combine pre-built technology modules to create customized solutions for their specific needs.
The platform encompasses a wide range of capabilities, including smart surveillance systems that can monitor production quality in real-time, connected vehicle solutions for logistics and supply chain optimization, and private 5G networks that provide the high-speed, low-latency connectivity that advanced IIoT applications require.
What makes this approach particularly valuable is that it dramatically reduces the time, cost, and complexity associated with IIoT implementation. Instead of spending months or years developing custom solutions, manufacturers can rapidly deploy proven technologies and focus their resources on optimizing operations rather than building infrastructure.
The implications of this plug-and-play approach extend far beyond individual implementations. By making advanced IIoT capabilities more accessible, platforms like this are democratizing industrial transformation and enabling smaller manufacturers to compete with much larger organizations.
As we look toward the future, the convergence of all these trends – intelligent machines, collaborative robotics, agentic AI, and plug-and-play platforms – is creating unprecedented opportunities for manufacturing innovation. We’re entering an era where the limiting factor in manufacturing isn’t technology capability, but rather imagination and strategic vision.
The manufacturing CIOs who are leading this transformation understand that IIoT isn’t just about implementing new technology – it is about reimagining what manufacturing can become. They’re creating organizations that are more resilient, more efficient, more sustainable, and more responsive to customer needs than ever before.
For you, whether you are working in manufacturing, considering a career in industrial technology, or simply interested in understanding how the products you use every day are made, this transformation represents a fundamental shift in how our physical world is created and maintained.
The decisions being made today about IIoT implementation, workforce development, and technology investment will shape the manufacturing landscape for decades to come. We are witnessing the birth of a new industrial age where human creativity and artificial intelligence combine to create possibilities that neither could achieve alone.
The journey ahead will undoubtedly present challenges, but the potential rewards – for businesses, workers, and society as a whole – are extraordinary. As we continue to push the boundaries of what is possible in manufacturing, we are not just building better factories – we’re creating the foundation for a more prosperous, sustainable, and innovative future.
And with that inspiring vision, we reach the end of today’s exploration into the fascinating world of IIoT transformation in manufacturing. We hope this deep dive has given you new insights into how technology is reshaping one of humanity’s most fundamental activities – the creation of the physical goods that define our modern world.
Thank you for joining us on this journey through the cutting-edge world of industrial transformation. Keep exploring, keep learning, and remember that the future of manufacturing is being built right now by the innovative minds who dare to imagine what’s possible when human ingenuity meets artificial intelligence.
We will be back next week with another thought-provoking episode that explores the technologies shaping our tomorrow. Until then, take a moment to appreciate the incredible sophistication behind every manufactured product you encounter – and the brilliant minds working to make it even better!